Although still a very young technology, I have had the pleasure (usually) of using three different types of so-called “additive manufacturing” technologies. My first experience with 3D printing was a major part of my ME 444 (toy design) class that ended with printing parts on a SLA 250 (3D systems). This was followed by using a Objet (now Stratasys) Eden350 as part of the Moonboot Plaque project and the RFID case project shown below (thanks to Paul Gemberlein). And finally, most of my printing has been done on a MakerBot Replicator 2 (and 2X) using their slicer.
- SLA 250
- Objet Eden350
- MakerBot Replicator 2
As a Co-Founder of the Purdue 3D printing Club, I not only leveraged my previous experience in growing new student organizations, but was also able to use my design and materials experience with three different technologies: SLA, polyjet, and FDM respectively.
Project: Active RFID Case
The 3D Printing Club (3DPC) was approached by the MED Institute to help flesh out a concept they had for an active RFID chip they were developing to help customers track products in the field. My role became to help communicate technical and manufacturing limitations from our MED contact to the other two members from the club working on the project ( to speak “industry” if you will). This included knowledge of the circuitry’s physical limits, final assembly procedures, and case material thermal and RF transmissivities. I also lent my engineering knowledge to avoid stress concentrators in our case design and my unique ability to know when a design requires literally a millimeter here or there sans measurement.
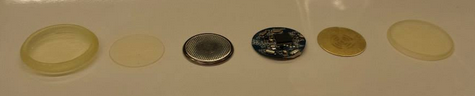
Case prototype showing use with battery, active RFID transmitter, and speaker plate
Our case design included an heat sink stand-in spacer (2nd from left), and two clasping halves and was iterated on the Object polyjet printers before presenting our final resin-simulant mockups (the final version was to be injection molded) and CAD files to MED. They were quite pleased with the final result both in quality of design (tolerances were design with final production technique in mind) but also because our work was able to save them considerable time and money versus doing it in-house.
Project: Custom Cases for SIGBOTS
As the size and importance of the custom circuitry used in our robots increased from one year to another, we eventually became worried that our creations might become damaged or tangled as part of normal use and gameplay. In order to preserve both the hardware and the aesthetics of our robots I created custom ABS cases based on the hardware prototypes. This allowed the case to be revised as the electronics were and for additional branding space. These cases were created for (initially) two types of boards: power supplys and radius arrays (see Project: Watchdog).
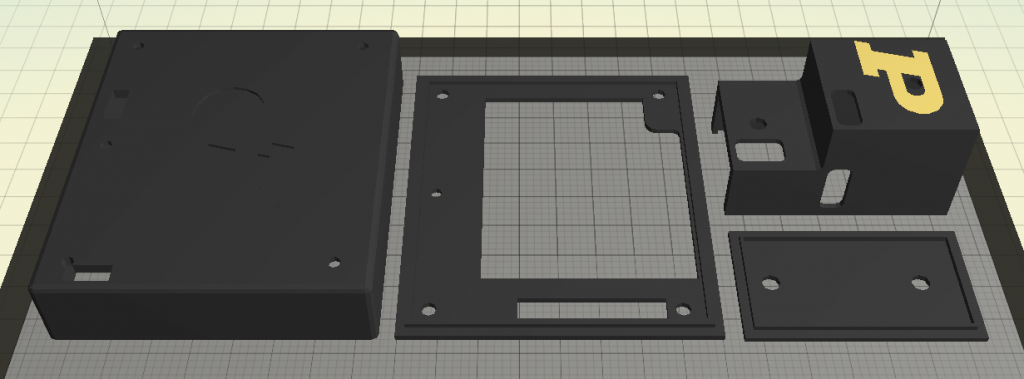
The case for the radius array (L) and power supply (R)
The cases were designed to fit the unique geometry of each board, ensuring wires stayed firmly seated and LED indicators were visible, all while adding collision protection and cable management. The bottom plate of the radius array case seen above includes a large oddly-shaped space in order to allow the bottom of the board to see the floor that it was designed to watch for reflectivity differences. The yellow (actually printed in gold) was printed separately (for time) and then fused to the larger piece with acetone, hence the choice of ABS over PLA. Details not shown include minor fillets on interior edges, outer edge reinforcement on the inside of all holes, and strongly filleted edges near connectors and wires. Everyone in the club as well as those at competitions have been impressed with the thoughtfulness of the design and it has since been passed down to continue to be updated with the underlying hardware.