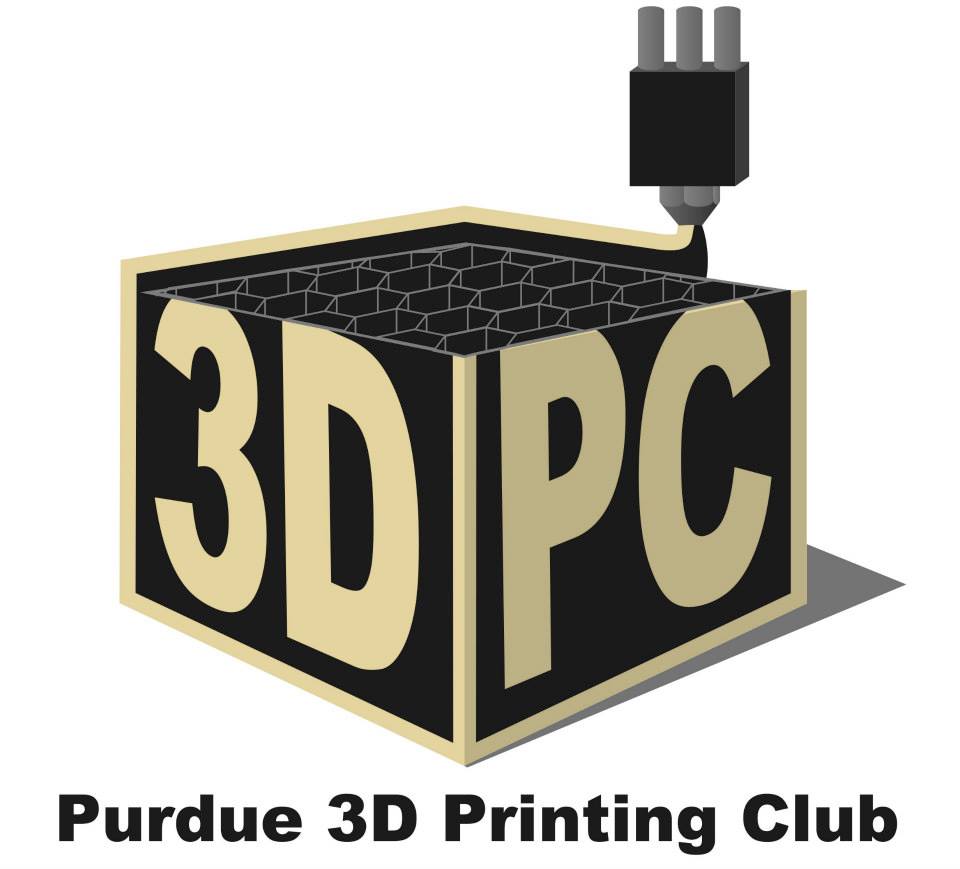
3D Printing Club
SO MANY PRINTERS SO LITTLE TIME
Fellow enthusiasts and I decide that if there are this many of us with interest, might as well start a club for everyone else too.
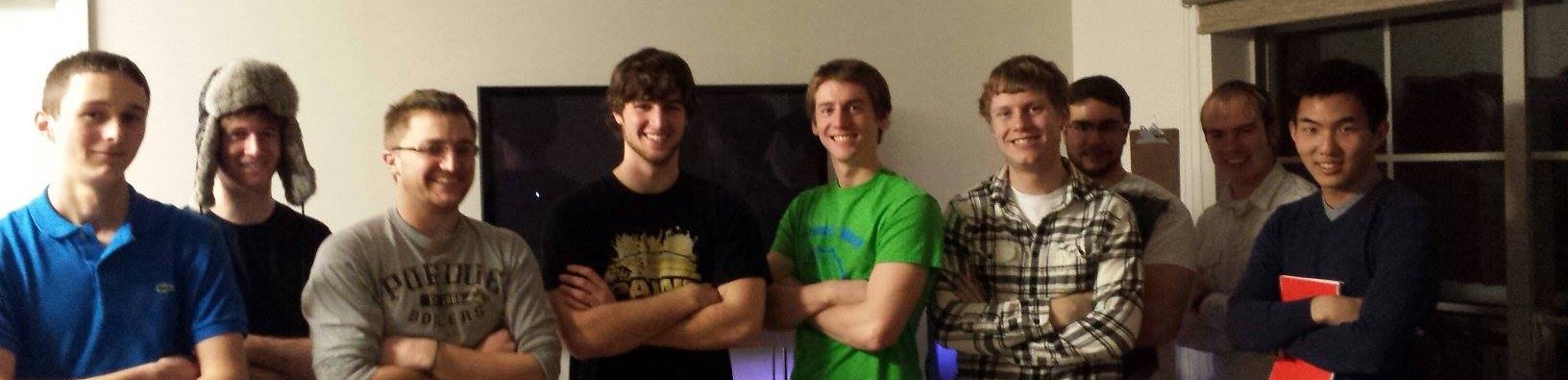
In 2013 some fellow 3D printing nerds (it’s ok when I say it) and I decided we couldn’t be the only ones interested in the emerging technology and decided to form a club. Some already had printers of there own (built or bought) either for personal use or graduate research. I helped lead the club until graduation, and I’d say they’re doing well continuing to work on community and personal projects.
Club printers in 2014: Objet Eden350 (Purdue), Makerbot Replicator 2 (club and new 3D printing lab had many), plus Makerbot 2X and Mendel Prusa and a few others privately owned
Special thanks to Ryan Kung, James Calteaux, and Clayton Patton
The 3D Printing Club (3DPC) was approached by the MED Institute to help flesh out a concept they had for an active RFID chip they were developing to help customers track products in the field. My role became to help communicate technical and manufacturing limitations from our MED contact to the other two members from the club working on the project (to speak “industry” if you will). This included knowledge of the circuitry’s physical limits, final assembly procedures, and case material thermal and RF transmissivities. I also lent my engineering knowledge to avoid stress concentrators in our case design and my unique ability to know when a design requires literally a millimeter here or there sans measurement.
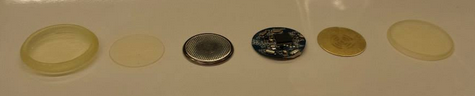
Case prototype showing use with battery, active RFID transmitter, and speaker plate
Our case design included an heat sink stand-in spacer (2nd from left), and two clasping halves and was iterated on the Object polyjet printers before presenting our final resin-simulant mockups (the final version was to be injection molded) and CAD files to MED. They were quite pleased with the final result both in quality of design (tolerances were designed with final production technique in mind) but also because our work was able to save them considerable time and money versus doing it in-house.